-
Syed Rashid Ahmed ButtShaanxi Chengda Industrial Furnace Co., Ltd. completed the commissioning of electric arc furnace, the workers carefully cooperated with Chengda engineers to learn and operate the equipment, showing the deep friendship and excellent cooperation between the people of China and Pakistan.
-
AboubacarAfter more than 1 month of intense production and debugging, 2 sets of heat exchange flue gas settling chamber equipment has been successfully put into operation ~ All the personnel involved in the project have worked hard! ~
-
Ji-hwan【 Warm congratulations 】 Shaanxi Chengda Industrial Furnace Manufacturing Company in South Korea, North Chungcheong County precious metal smelting furnace equipment installation and careful manufacturing and strict commissioning, looking forward to the future in more fields to achieve mutually beneficial win-win cooperation!
Smeling Industrial Tailings Equipment(New)
Place of Origin | Shaanxi, China |
---|---|
Brand Name | Shaanxi Chengda |
Certification | ISO9001 |
Model Number | Negotiate based on equipment processing capacity |
Minimum Order Quantity | 1set |
Price | The price will be negotiated based on the technical requirements and supply scope of Party A |
Packaging Details | Discuss according to the specific requirements of Party A |
Delivery Time | 2~3 months |
Payment Terms | L/C,D/A,D/P,T/T,Western Union,MoneyGram |
Supply Ability | Complete production supply chain, supply on time, and meet quality standards |
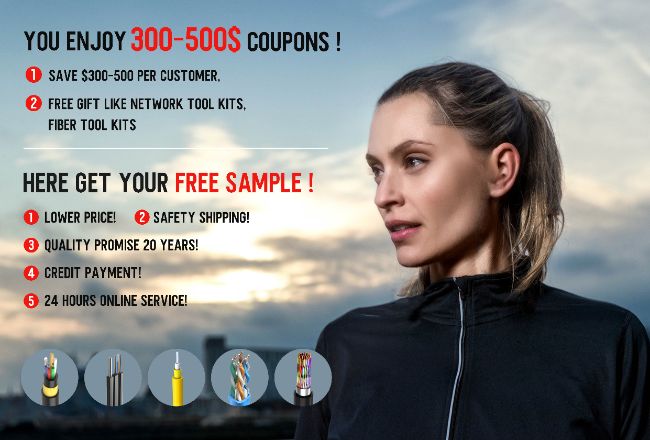
Contact me for free samples and coupons.
WhatsApp:0086 18588475571
WeChat: 0086 18588475571
Skype: sales10@aixton.com
If you have any concern, we provide 24-hour online help.
xDelivery Standard | New | Core Component Shelf Life | 1year |
---|---|---|---|
Type | Industrial Tailings | Country Of Origin | Shaanxi, China |
Highlight | Industrial Tailings,Industrial Tailings,Industrial Tailings |
The main types of tailings electric furnaces in the smelting industry include electric arc furnaces, submerged arc furnaces, etc. The following is a detailed introduction to them:
Electric arc furnace:
Working principle: Utilizing the high temperature generated by the arc between the electrode and the furnace material to melt and smelt tailings materials. When current passes through the electrode, an arc is formed between the electrode end and the furnace charge, and the high temperature generated by the arc can reach over 3000 ℃, causing the furnace charge to quickly melt and undergo chemical reactions.
Characteristics: Electric arc furnaces have the advantages of fast heating speed, precise temperature control, and easy adjustment of furnace atmosphere. They can adapt to the smelting needs of different types of tailings and produce high-quality metal products. At the same time, the automation level of electric arc furnaces is relatively high, and the production process is easy to achieve mechanization and automation, which can effectively improve production efficiency and product quality, and reduce labor intensity. However, electric arc furnaces consume a large amount of electricity and have a significant impact on the power grid, requiring corresponding reactive power compensation devices and voltage stabilizers.
Submerged arc furnace:
Working principle: also known as electric arc furnace or resistance electric furnace, mainly used for reducing and smelting ores, carbonaceous reducing agents, solvents and other raw materials. It uses carbon or magnesium refractory materials as furnace lining, uses self baking electrodes, and inserts the electrodes into the furnace material for submerged arc operation. It uses the energy of the arc and the energy generated by the resistance of the furnace material when the current passes through the furnace material to melt the metal.
Features: The ore blast furnace has the advantages of high production capacity, low energy consumption, and stable product quality, and is suitable for large-scale production of ferroalloys, calcium carbide, and other products. It can process various types of tailings resources, extract valuable metals from them, and achieve resource recycling and utilization. In addition, the operating cost of the mineral thermal furnace is relatively low, the production process is relatively stable, and it is easy to achieve automation control. However, the investment in mineral thermal furnaces is relatively large, the construction period is long, and the requirements for the quality and particle size of raw materials are high.