-
Syed Rashid Ahmed ButtShaanxi Chengda Industrial Furnace Co., Ltd. completed the commissioning of electric arc furnace, the workers carefully cooperated with Chengda engineers to learn and operate the equipment, showing the deep friendship and excellent cooperation between the people of China and Pakistan.
-
AboubacarAfter more than 1 month of intense production and debugging, 2 sets of heat exchange flue gas settling chamber equipment has been successfully put into operation ~ All the personnel involved in the project have worked hard! ~
-
Ji-hwan【 Warm congratulations 】 Shaanxi Chengda Industrial Furnace Manufacturing Company in South Korea, North Chungcheong County precious metal smelting furnace equipment installation and careful manufacturing and strict commissioning, looking forward to the future in more fields to achieve mutually beneficial win-win cooperation!
HZX-5000 Series Electric Arc Furnace Solution For Solid And Dangerous Waste
Place of Origin | Shaanxi, China |
---|---|
Brand Name | Shaanxi Chengda |
Certification | ISO9001 |
Model Number | DC electric arc furnace - Solid and dangerous waste |
Minimum Order Quantity | 1set |
Price | Prices and models are negotiable |
Delivery Time | 8-15work days |
Payment Terms | L/C, D/A, D/P, T/T, Western Union, MoneyGram |
Supply Ability | 5set per month |
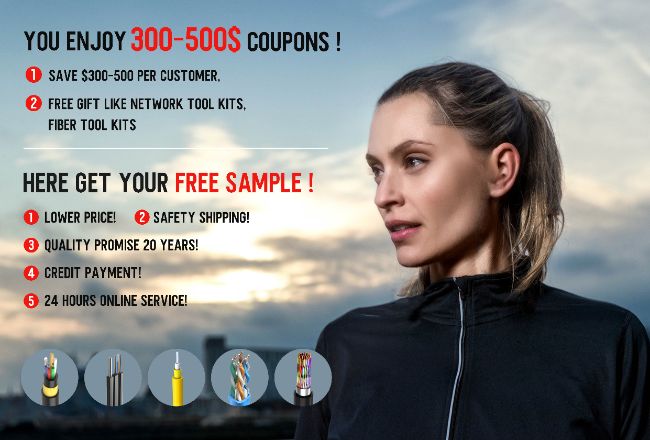
Contact me for free samples and coupons.
WhatsApp:0086 18588475571
WeChat: 0086 18588475571
Skype: sales10@aixton.com
If you have any concern, we provide 24-hour online help.
xCountry Of Origin | Shaanxi, China | Condition | New |
---|---|---|---|
Core Component Warranty | 1years | Sale-type | Popular Product |
Highlight | HZX-5000 electric arc furnace,Waste electric arc furnace,Solid Waste eaf furnace |
HZX-5000 series DC electric arc furnace - Solid and dangerous waste
Rock wool, mineral wool industry status:
Industrial waste disposal has always been the focus of attention of domestic and foreign enterprises. In 2018, the state promulgated the solid waste discharge standards, how to deal with industrial waste, how to comprehensively utilize industrial waste has become a problem faced by domestic enterprises. The hot industrial waste slag contains a lot of sensible heat, according to statistics (taking blast furnace slag, silicon manganese alloy slag, nickel iron slag as an example) each ton of hot slag containing waste heat is about 50KG of standard coal generated heat, each ton of hot slag waste heat can generate electricity about 90KW·h ~ 100KW·h, how to use this part of sensible heat is our research direction.
Mineral wool (or rock wool) is a kind of artificial inorganic fiber, it has light weight, small thermal conductivity, strong heat resistance and non-combustible and other excellent properties. This is commonly used insulation materials, such as vermiculite, perlite, diatomite, foam cement, etc., is difficult to fully compare with it. Mineral (rock) cotton adding a special binder can be made of flexible or semi-rigid products, such as mineral wool shell, mineral wool board, mineral wool felt, etc. These products can be widely used in petroleum, electric power, metallurgy, chemical industry, construction and transportation and other industries, can also be used as sound absorption and sound insulation materials.
Hot melt slag production process of mineral wool:
The advantages and disadvantages of producing mineral wool and rock wool by electric furnace:
Advantages:
(1) The equipment has strong applicability, easy to start, stop, power off, etc., simple operation;
(2) Equipment investment is relatively small, easy to repair and maintain;
(3) High heating efficiency (heating temperature can reach more than 2000℃);
(4) Low energy consumption (compared to the traditional process saving 300Kg ~ 350Kg coke);
(5) High working efficiency, can work continuously for 24 hours, do not need frequent furnace shutdown;
(6) The requirements for raw materials (generally require raw material particles in 1mm-5mm);
(7) The production waste can be reused, and the waste slag treatment rate can reach more than 90%;
(8) Low environmental requirements, less flue gas emissions (mainly smoke 350mg/m²), easy to recycle.
Cons:
(1) High one-time investment;
(2) Add mixing material with hot slag production, which is not easy to melt evenly;
(3) The lining life is short (generally 3 months -4 months repair).
Key technical process: